While waiting for an affordable CNC lathe I have been using a technique of threading on a manual lathe that allows threading at high speed up from a shoulder both external and internal right hand threads.
First let's explore the usual way to turn an external right hand thread on a lathe. The spindle is rotating counter clock wise, the feed is toward the headstock and the tool is mounted right side up facing away from the operator. A shoulder is on the left so when threading towards the headstock the operator must stop the threading process near the shoulder. Typically there is a groove cut to the right of the shoulder twice the thread depth and at least one thread pitch in width. If turning an inch pitch thread with a lathe with an inch pitch leadscrew then one can open the half nut at the shoulder. If threading a metric pitch thread on a lathe with an inch leadscrew then the half nut cannot be opened. The real problem here is that it is really hard to stop the lathe spindle very quickly or open the half nut quickly. The lowest speed on a typical small lathe is 75rpm. At 75 rpm with a coarse thread pitch it is often difficult and frightening to stop the thread turning quickly enough as the shoulder is approached.
Here is where the reverse helix method comes into play allowing one to thread at high speed up from a shoulder. Using the reverse helix method the spindle rotates CW with feed towards the tailstock. This means there is plenty of time to stop the lathe at the end of a threading pass. For an external RH thread using the reverse helix method the tool is mounted upside down facing away from the operator or mounted right side up on a rear toolpost facing the operator. I chose to mount my tool upside down on a regular toolpost. I use carbide inserts when thread turning and typically use a full topping insert for the particular thread pitch. That way I get perfect thread form and the OD is concentric with the PD. For example I threaded a 2.5-20UN thread in 6061-T6 aluminum up from a shoulder. Minimum recommended spindle speed was 400 rpm and I cut the thread at 500rpm. At this speed it would have been very difficult to stop the lathe before crashing into the shoulder using the normal threading method. Using the reverse helix method thread turning up from a shoulder was easy and there was plenty of time to stop the lathe at the end of each threading pass. The tool used was a AL050-3LH insert was a 3EL20UN and thread anvil was a YI3-2N. Thread finish is excellent with no burrs and no other operations required. The chip from thread turning at 500 rpm came out as a continuous chip as shown in the photo below.
Reverse helix internal RH thread turning is done in a similar way except the tool in held upright in a AVR075-3LH toolholder, 3IL20UN insert, and YE3-2N anvil. The tool is facing away from the operator and bearing against the inside wall opposite the operator. The internal reverse helix method is shown in a photo below.
Note: I have a D1-4 camlock spindle on my Graziano SAG12 lathe which allows for a mounted chuck to run in reverse. If using a chuck mounted in a threaded spindle some precaution must be used when running in reverse to prevent the chuck from spinning off.
The reverse helix method has allowed me to thread turn at very high speed up from a shoulder on my manual lathe resulting in much better surface finish using carbide insert tooling.
The same method can be used with a CNC lathe only with a CNC lathe there are other options available such as using the alternative flank method of tool infeed so that the carbide insert wears evenly on both sides of the cutting surface.
Don
![]()
![]()
![]()
First let's explore the usual way to turn an external right hand thread on a lathe. The spindle is rotating counter clock wise, the feed is toward the headstock and the tool is mounted right side up facing away from the operator. A shoulder is on the left so when threading towards the headstock the operator must stop the threading process near the shoulder. Typically there is a groove cut to the right of the shoulder twice the thread depth and at least one thread pitch in width. If turning an inch pitch thread with a lathe with an inch pitch leadscrew then one can open the half nut at the shoulder. If threading a metric pitch thread on a lathe with an inch leadscrew then the half nut cannot be opened. The real problem here is that it is really hard to stop the lathe spindle very quickly or open the half nut quickly. The lowest speed on a typical small lathe is 75rpm. At 75 rpm with a coarse thread pitch it is often difficult and frightening to stop the thread turning quickly enough as the shoulder is approached.
Here is where the reverse helix method comes into play allowing one to thread at high speed up from a shoulder. Using the reverse helix method the spindle rotates CW with feed towards the tailstock. This means there is plenty of time to stop the lathe at the end of a threading pass. For an external RH thread using the reverse helix method the tool is mounted upside down facing away from the operator or mounted right side up on a rear toolpost facing the operator. I chose to mount my tool upside down on a regular toolpost. I use carbide inserts when thread turning and typically use a full topping insert for the particular thread pitch. That way I get perfect thread form and the OD is concentric with the PD. For example I threaded a 2.5-20UN thread in 6061-T6 aluminum up from a shoulder. Minimum recommended spindle speed was 400 rpm and I cut the thread at 500rpm. At this speed it would have been very difficult to stop the lathe before crashing into the shoulder using the normal threading method. Using the reverse helix method thread turning up from a shoulder was easy and there was plenty of time to stop the lathe at the end of each threading pass. The tool used was a AL050-3LH insert was a 3EL20UN and thread anvil was a YI3-2N. Thread finish is excellent with no burrs and no other operations required. The chip from thread turning at 500 rpm came out as a continuous chip as shown in the photo below.
Reverse helix internal RH thread turning is done in a similar way except the tool in held upright in a AVR075-3LH toolholder, 3IL20UN insert, and YE3-2N anvil. The tool is facing away from the operator and bearing against the inside wall opposite the operator. The internal reverse helix method is shown in a photo below.
Note: I have a D1-4 camlock spindle on my Graziano SAG12 lathe which allows for a mounted chuck to run in reverse. If using a chuck mounted in a threaded spindle some precaution must be used when running in reverse to prevent the chuck from spinning off.
The reverse helix method has allowed me to thread turn at very high speed up from a shoulder on my manual lathe resulting in much better surface finish using carbide insert tooling.
The same method can be used with a CNC lathe only with a CNC lathe there are other options available such as using the alternative flank method of tool infeed so that the carbide insert wears evenly on both sides of the cutting surface.
Don
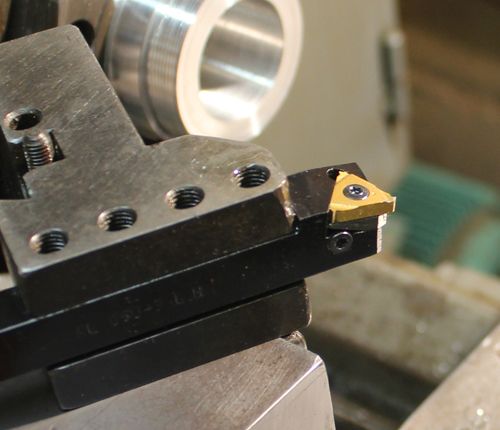
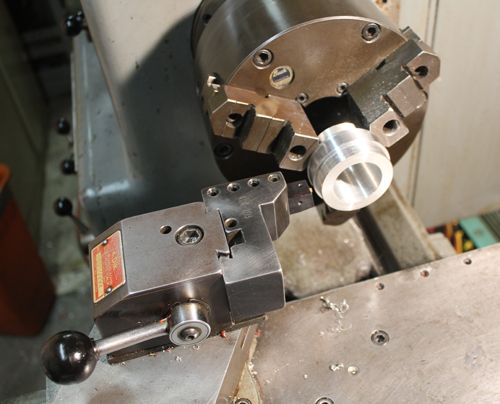
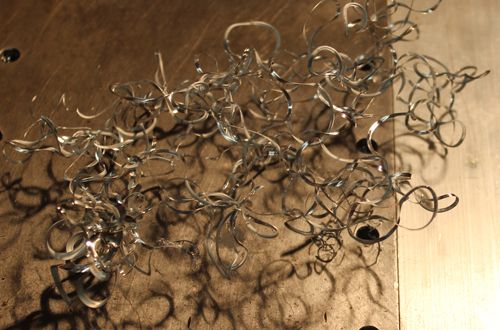
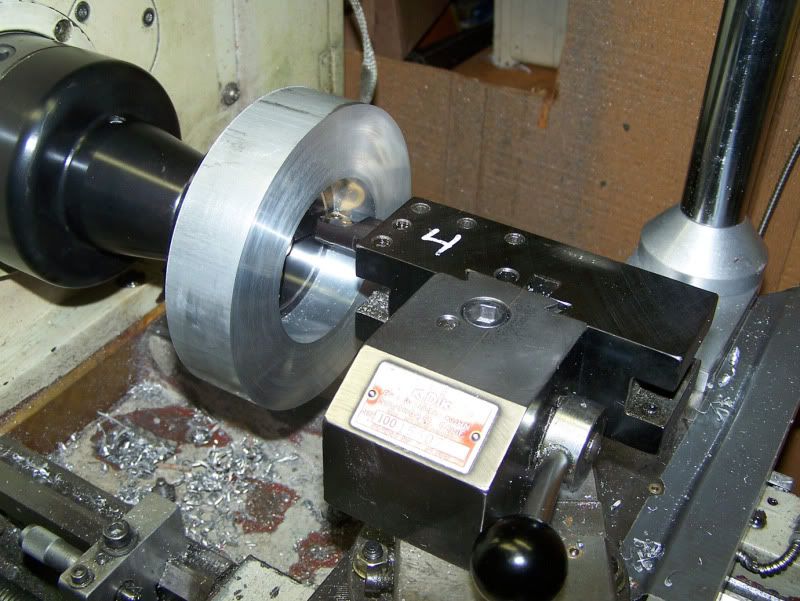